There is nothing more important on a job site than safety. To prevent an injury, one must recognize the potential risk and take mitigative action beforehand. The challenge that companies like us face is not so much trying to figure out how an incident happened, but training employees to recognize the potential of injury before it happens. Once that mindset has been ingrained, team members must be empowered to address and escalate it without repercussion.
This train of thought is a cultural shift for many companies, as it was for us. The term safety has become synonymous with construction and is often enforced, or incentivized, as a separate component that must be done in addition to everyday tasks.
What if safety was so baked into a culture that an individual could not distinguish his or her job task from continuous risk assessment?
At Brennan, we have worked for years to make work tasks and safety indistinguishable. The program we have adopted is called the Safety-Based Observation Program (SBO), which is a corporate-wide process that has had three major results.
- Safety is kept at the forefront of everyone’s mind
- Observations allow us to identify and share leading indicators of potential hazards
- Driven safety management statistics to ideal levels
The Basics of our SBO Program
Observe & Record
When we began the SBO program we tied it to our bonus program to motivate individuals to participate. We kept it simple by requiring every employee to make a minimum number of observations per quarter. As the program evolved we found that employees began to participate more than the minimum because they could see that their observations were contributing to improvements in the way we do things. Managers were listening, and the observations were being taken very seriously. We also made it easy for them to submit information. We worked closely with HCSS to develop a safety app that employees could download onto their smartphones and tablets. It only takes a couple of minutes to record and submit an observation directly to our Safety Department.
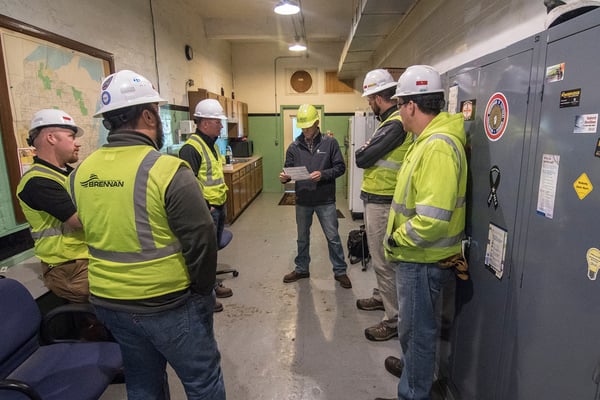
Here’s how it works:
The SBO process consists of completing four steps in the following order:
1. General information
The observations are not anonymous so names, dates, job site info are all required.
2. Positive or Negative
Is the observation positive or negative? If negative it gets flagged and addressed immediately. Positive observations are often commended during a weekly safety stand down.
3. Risk Rating
The action is then given a risk rating from 1-5, with 5 being the highest. Anything ranked 3 or higher is automatically forwarded directly to the appropriate safety personnel.
4. Cause
Employees determine the cause from three categories, unsafe act, unsafe condition, and unsure. This helps us statistically categorize the observation as an environmental factor or as human error.
5. Type
The last category is for describing the type of action and includes options such as caught in/on/or between, electrical, environmental, equipment related, fall/slip/trip, other, overexertion, struck by/struck against, and utility. This is another place we can categorize the observation.
6. Description and Images
The form also contains a description box where employees can detail their observations more thoroughly. Up to ten pictures can be easily included to give visual examples.
Using the Data
Every SBO that is submitted in the field is collected by our safety department and categorized. It is also included in our weekly safety reports that are sent out company-wide every Monday. We review select SBOs on a weekly basis during our corporate safety meeting held every Monday. These meetings include all levels of our employees starting at the highest level of management, down to the newest team members. We also welcome the inclusion and participation of any subcontractors, vendors, site visitors, and clientele.
Though many of the negative observations have been addressed at this point, discussing them allows us to share solutions. This discussion also allows us to create awareness on issues that may have otherwise gone unnoticed on other job sites. The discussion is constructive and participation from all levels is required.
The Results
The biggest change that our SBO program has brought is a shift in culture. Individuals are constantly looking for infractions, which makes them more aware of their surroundings. We have created a blame-free environment where the infraction can be corrected without negatively affecting the individual, his or her manager, or the outcome of the project. Stopping work for safety is not viewed as a bad thing, and often the individual who does so is commended. As culture and corrective action can be a hard thing to statistically measure, we often reflect the success of the program by listing our safety management statistics.
Among the most notable improvements from implementing our SBO program is the improvement in our safety metrics, including our Total Recordable Incident Rate (TRIR), Lost Time Incident Rate (LTIR), and Experience Modification Rate (EMR). Currently, both our TRIR and LTIR sit at 0.0 as we approach the end of 2018. In fact, we are approaching 6 years without a lost-time injury!
EMR is a number assigned by insurance companies that measures the chances of future risk by looking at the cost of injuries over the last three years. This rate can vary by company size, the number of employees, and other risk factors. The only standard is that the average EMR rate for a construction company is 1.0.
EMR rates adjust more slowly because it is an average taken over three years. Since the inception of our SBO program, we have lowered our EMR to 0.51, which is the lowest possible rate that we can currently achieve according to our insurance company. This low score translates to tens of thousands of dollars in insurance costs (not to mention personal injury costs)!
Year |
Brennan’s EMR Score |
---|---|
2018 |
0.51 |
2017 |
0.52 |
2016 |
0.62 |
2015 |
0.61 |
2014 |
0.58 |
Luck has Nothing to do with it
We often hear the comment that it takes luck to achieve perfect safety results. There is no doubt that accidents can happen, however, if every individual on a job site is trained to analyze the situation before every task, is given the opportunity to actually stop work for safety, and is given the ability to escalate concerns over his or her superiors, then far less can be chalked up to "luck." Every day we have people out working in dangerous conditions, above dams, underwater, around hazardous waste, near railroad tracks, and more. We do not chalk our success up to luck, but we also know that we cannot be complacent for one minute.
For more information on Brennan's safety program, visit our Safety page or contact us directly.